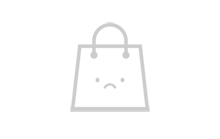
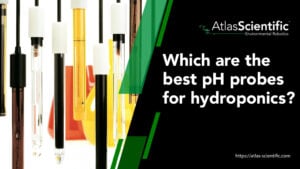
Best pH Probes For Hydroponics in 2025 – A Complete Buying Guide
Finding the best pH probe for hydroponics can make or break your growing success. In hydroponics, maintaining the correct pH is essential because it directly
# Type at least 1 character to search # Hit enter to search or ESC to close
No products in the cart.
No products in the cart.
Product Categories
An RTD sensor measures temperature by correlating the resistance of the sensor element with temperature changes. Made from pure metals like platinum, RTDs provide accurate and stable readings, making them ideal for industrial, laboratory, and environmental temperature monitoring.
Temperature measurement stands as a cornerstone of modern industrial processes, where accuracy can mean the difference between success and failure. A resistance temperature detector (RTD) offers unbeaten precision and stability compared to other temperature measurement methods, making it essential equipment across industries from pharmaceutical manufacturing to food processing.
In this article, we will explore the fundamental principles behind RTD temperature sensors and their practical applications. From basic operating principles to advanced installation techniques, to help you understand how these complex temperature probes work.
Whether you’re new to temperature measurement or seeking to deepen your technical knowledge, this guide will equip you with the essential understanding of resistance temperature detector technology.
The core principle of a resistance temperature detector operates on a fundamental physics concept: metals’ electrical resistance increases as temperature rises. When we pass a small electrical current through an RTD sensor, the resistance changes predictably with temperature variations. This relationship is remarkably linear, especially between 0°C and 100°C, making RTD temperature sensors highly reliable for precise measurements.
The journey of RTD technology began with Sir William Siemens’s groundbreaking proposal in 1871. We can trace how his introduction of platinum as an RTD element revolutionized temperature measurement. Modern RTDs have evolved significantly, and we now see three main categories:
Component | Function | Material Choice |
Sensing Element | Temperature detection | Platinum, Nickel, or Copper |
Protective Sheath | Environmental protection | Stainless Steel or Inconel |
Lead Wires | Signal transmission | Insulated copper with Teflon/fiberglass |
Connection Fittings | Process integration | Standard thermocouple fittings |
We’ve found that platinum has emerged as the preferred material for high-precision applications due to its exceptional stability and nearly linear resistance-temperature relationship.
When we examine modern RTD probes, we see they can maintain stability for many years, while offering quick response times typically between 0.5 and 5 seconds.
The evolution of these sensors continues with the integration of smart features. Self-diagnostic capabilities and wireless communication options are becoming increasingly common in industrial applications. These advancements allow us to monitor sensor health continuously and optimize energy consumption through improved power management features.
When selecting resistance temperature detectors for our applications, we must carefully consider the material properties and configuration options that best suit our specific needs. Let’s explore the key factors that influence our RTD sensor selection.
In our experience with RTD temperature sensors, we find that the choice of element material significantly impacts performance.
Material | Temperature Range | Key Characteristics |
Platinum | -200°C to 850°C | Most stable, highest accuracy |
Nickel | -80°C to 260°C | Lower cost, good corrosion resistance |
Copper | -100°C to 260°C | Economical, limited range |
At Atlas Scientific, our RTD temperature sensors are all made from high-quality platinum material.
We’ve found that RTD configurations play a crucial role in measurement accuracy. Our experience with different wire configurations reveals the following:
When selecting an RTD sensor, you consider several critical factors:
Sheathing material selection is also crucial – stainless steel serves well up to 500°F, while Inconel is better suited for higher temperatures up to 1200°F. For applications requiring rapid response, we often recommend thin-film RTDs due to their smaller size and faster temperature equilibration.
In industrial settings, we typically specify Class B tolerance for general applications, but when higher precision is needed, we move to Class A specifications. When helping you select an RTD temperature sensor we always consider the balance between accuracy requirements and cost constraints while ensuring long-term stability and reliability.
Our extensive experience with industrial temperature measurement, proper installation, and wiring of RTD sensors can make the difference between reliable readings and costly errors.
We’ve found that understanding the types of different configurations and mounting techniques is crucial for optimal performance.
When we install RTD temperature sensors, we carefully consider the wiring configuration based on the application requirements. Here’s how we compare the three main configurations:
Configuration | Accuracy | Best Used For | Lead Wire Effect |
2-Wire | Basic | Short distances (<10ft) | Most affected |
3-Wire | Good | Industrial applications | Partially compensated |
4-Wire | Excellent | Laboratory/precision | Fully compensated |
We’ve observed that while 2-wire configurations are simplest, they’re susceptible to lead wire resistance errors. Our experience shows that 3-wire configurations offer the best balance for most industrial applications, while we reserve 4-wire setups for situations demanding the highest accuracy.
In our installations, we’ve learned that thermal contact is critical for accurate temperature measurement. We follow these essential mounting practices:
Maintaining the accuracy of our resistance temperature detectors requires a systematic approach to calibration and regular maintenance.
We perform calibration through comparison calibration, where RTD temperature sensors are tested against certified Platinum Resistance Thermometers (PRTs). Our calibration process adheres to ISO 17025 standards and maintains traceability to international standards like ITS-90 through national laboratories.
Our maintenance approach focuses on preserving RTD sensor accuracy while preventing unexpected failures. We recommend these essential maintenance steps:
Unlike thermocouples, we’ve found that RTD sensors experience minimal drift, often eliminating the need for frequent recalibration. However, we still recommend periodic validation for critical measurements to maintain confidence in readings.
When temperature readings seem incorrect, first check for these typical problems:
TOP TIP: We’ve learned that most accuracy issues stem from installation problems rather than sensor failure. When troubleshooting, always start with connection verification and work systematically through potential issues before considering sensor replacement.
In today’s smart manufacturing environment, we’ve witnessed how resistance temperature detectors have become integral to process control and monitoring systems. Proper integration of these precise instruments can transform traditional manufacturing into data-driven operations.
Integrating RTD temperature sensors with modern control systems requires careful consideration of both hardware and software compatibility. Implementation typically involves:
Integration Aspect | Key Considerations | Benefits |
Signal Processing | 4-20mA or digital output | Noise immunity |
Control Interface | PLC/SCADA compatibility | Real-time control |
Communication Protocol | Industrial protocols (Modbus, Profibus) | Standardized data exchange |
When implementing RTD sensors in process control, ensure they communicate effectively with supervisory control and data acquisition (SCADA) systems. This integration allows you to maintain precise temperature control while enabling automated responses to process variations.
The best approach to data acquisition focuses on capturing accurate temperature measurements while ensuring data integrity. Implemented systems provide:
Proper RTD sensor integration significantly improves process optimization and safety.
In our transition to Industry 4.0, we’ve seen resistance temperature detectors evolve into smart sensors that form the backbone of IoT-enabled manufacturing. These implementation strategies focus on creating an interconnected, optimized, and scalable manufacturing ecosystem.
We’re particularly excited about how IoT has transformed traditional RTD temperature sensor applications. By incorporating wireless connectivity and edge computing capabilities, we can now:
The integration of RTD sensors with IoT platforms has revealed significant advantages in predictive maintenance. We can now detect potential equipment failures before they occur by analyzing temperature patterns and trends. This proactive approach has helped us achieve substantial cost savings and improved operational efficiency.
An RTD temperature sensor measures temperature by linking changes in the sensor’s resistance to variations in temperature. Constructed from pure metals like platinum, RTDs deliver precise and reliable readings, making them well-suited for industrial, laboratory, and environmental temperature monitoring.
RTD technology continues to advance, particularly in smart manufacturing environments. Our experience shows that successful temperature measurement projects depend on understanding both fundamental principles and details of practical implementation.
If you would like to learn more about RTD temperature sensors or would like to explore our comprehensive range of temperature probes and sensors, contact the world-class team at Atlas Scientific.
Finding the best pH probe for hydroponics can make or break your growing success. In hydroponics, maintaining the correct pH is essential because it directly
The fastest way to reduce ammonia levels in a fish tank is to perform partial water changes, temporarily stop feeding fish, use chemical filtration, increase