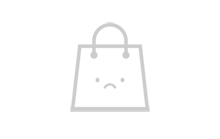
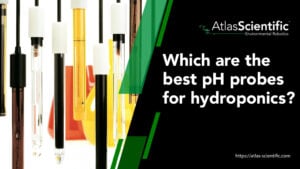
Best pH Probes For Hydroponics in 2025 – A Complete Buying Guide
Finding the best pH probe for hydroponics can make or break your growing success. In hydroponics, maintaining the correct pH is essential because it directly
# Type at least 1 character to search # Hit enter to search or ESC to close
No products in the cart.
No products in the cart.
Product Categories
One of the key differences between analog and digital sensors is their output resolution. For example, analog sensors provide infinite resolution since they provide a continuous range of values, while digital sensors have a finite resolution determined by the number of bits used to represent the signal. Another difference is the susceptibility to noise. Analog signals are more prone to noise interference since they are continuous and can be affected by external factors such as electromagnetic interference. On the other hand, digital signals, are less susceptible to noise since they are discrete and can be easily filtered and processed.
In today’s world, sensors play a crucial role in various industries and applications. They enable machines and devices to collect data from the environment, interpret it, and make informed decisions. When it comes to sensors, analog and digital are two common types that are used in various industries and applications. Understanding the key differences between these two types is crucial for choosing the right sensor for your specific needs.
In the past, analog sensors were the go-to choice for many applications. These sensors operate on a continuous scale, providing a smooth and accurate representation of the measured quantity. They were widely used in industries such as telecommunications, automotive, and aerospace. Analog sensors were particularly important because they allowed for precise measurements and control, ensuring the smooth functioning of various systems.
However, as technology progressed, digital sensors emerged as a game-changer. These sensors convert the measured quantity into discrete values, which can be easily processed by computers and other digital devices. Digital sensors offer several advantages over their analog counterparts, such as improved accuracy, reliability, and ease of integration with digital systems. They are now extensively used in fields like medical diagnostics, environmental monitoring, and smart home automation.
Analog sensors differ significantly from digital sensors and usually come with fewer features. These sensors generate what is called an analog signal, a continuous signal representing a quantity.
While analog sensors sacrifice some efficiency for a more continuous and slightly more accurate signal, their feature set doesn’t match up to that of digital sensors. However, when using analog sensors, you can have greater confidence in the readings you receive.
Analog quantities known for their continuous nature include speed, pressure, displacement, strain, and temperature. For example, when measuring a liquid’s temperature with a thermometer, the analog sensor provides continuous readings. This means it promptly responds to any changes in the liquid’s temperature as it either heats up or cools down.
There are various types of analog sensors, and one of the most common is the pressure sensor. It finds widespread use in industrial and laboratory settings to regulate the pressure of liquids or gases. Pressure is typically gauged by determining the force per unit area. These sensors, functioning as transducers, produce a signal in response to applied pressure.
Pressure sensors serve the purpose of monitoring and controlling a multitude of applications. Facilities can employ these sensors to indirectly gauge variables such as gas and fluid flow, water level, speed, and altitude. It’s worth noting that pressure analog sensors might also be known as pressure transducers, pressure senders, pressure transmitters, and pressure indicators.
Analog sensors find applications in a wide range of industries and systems, such as:
For example, in the automotive industry, analog sensors are used to monitor engine temperature, tire pressure, and airbag deployment.
In the healthcare sector, they are utilized in devices like electrocardiograms (ECGs), blood pressure monitors, and pulse oximeters.
Digital sensors measure physical quantities and convert them into a digital signal. Unlike analog sensors, digital sensors provide discrete output signals that are represented by binary values, usually ones and zeros (1s and 0s). Digital sensors use algorithms and digital processing to interpret their inputs and generate the desired output and often employ additional components like analog-to-digital converters (ADCs) to convert analog signals into digital format. An example of ADCs are temperature sensors as although they are a digital tool, they interpret signals via an analog input.
Digital sensors excel at recording diverse measurements, such as pH, conductivity, dissolved oxygen, and the concentration of ammonia and nitrate. While traditional digital sensors provide reliable and highly accurate results, a newer generation, known as smart sensors, is gaining prominence. These advanced digital sensors are becoming increasingly popular due to their ability to modernize measurements through wireless and digital communication.
Smart sensors represent a contemporary and feature-rich evolution of the digital sensor. Typically, smart sensors offer more accurate and fully automated data collection, reducing the chances of errors. Smart devices are widely used in monitoring applications, especially in fields like water treatment systems, exploration work, and smart grids.
The essential components of a smart sensor include the main sensor, a microprocessor, and some form of communicational technology.
It’s important to note that a smart sensor requires computational resources. If a sensor can only transmit data from one location to another for remote processing, it does not qualify a sensor as “smart.” Add-on components that can be integrated into a smart sensor include analog filters, amplifiers, and transducers. These sensors often include software elements in their design, enabling functions such as data conversion, digital processing, and communication with external devices.
Five common types of smart sensors employed in industrial settings are:
Level sensors measure the volume space in a container, enabling applications like fuel level monitoring in vehicles.
Pressure sensors monitor a pipeline’s fluid and gas pressure, issuing warnings in the event of pressure fluctuations indicating flow control issues or leaks.
Temperature sensors monitor component temperatures to prompt corrective actions, crucial in industrial settings to prevent machinery overheating.
Infrared sensors come in various forms, including thermal imaging cameras or non-contact infrared thermometers for temperature monitoring. Others function as optical sensors tuned to specific frequencies, commonly used in medical equipment like pulse oximetry devices.
Proximity sensors detect an object or individual’s location concerning the sensor, applicable in retail settings to track customer movements within a store.
Digital sensors find widespread applications in various fields including:
As mentioned above, analog sensors generate a continuous output signal or voltage that is directly proportional to the quantity it is designed to measure. These sensors produce analog output and are particularly suited for measuring continuous, variable quantities such as temperature, speed, displacement, pressure, and strain.
Analog quantities are characterized by their continuous and smooth transitions, making them well-suited for applications where a constant and nuanced response is required.
For example, the temperature of a liquid can be accurately measured using analog sensors like a thermometer or thermocouple. These devices continuously and responsively register changes in temperature as the liquid undergoes heating or cooling processes, reflecting the seamless nature of analog measurements in capturing dynamic variations in physical parameters.
On the other hand…
Digital sensors, in contrast to their analog counterparts, offer advantages by overcoming inherent limitations associated with continuous signals. These sensors find widespread application in diverse fields, including wastewater treatment, water management, and various industrial processes. Comprising the sensor itself, a connecting cable, and a transmitter, digital sensors provide a comprehensive and efficient solution for precise data acquisition.
Examples of parameters routinely measured using digital sensors include pH level, conductivity, dissolved oxygen, ammonium, and nitrate levels, showcasing the adaptability and accuracy of digital technology in capturing and conveying information in industrial and environmental contexts.
Factors | Analog Sensors | Digital Sensors |
Signal | Continuous signals from physical measurements | Discrete-time signals from digital modulation |
Bandwidth | Consumes less bandwidth as these sensors measure in real-time | They consume more bandwidth as there is no guarantee the signal can be processed in real-time |
Waves | Sine waves | Square waves |
Data transmissions | Subject to deterioration by noise during transmission | Can be noise-immune without deterioration during transmission |
Noise response | Noise can affect accuracy | Less affected by noise than analog sensors |
Flexibility | Not flexible | Digital hardware is flexible |
Memory | Stored as a wave signal | Stored as a binary bit |
Cost | Low-cost | High-cost |
Portability | Portable | Not portable |
Power requirements | Draws a large amount of power | Draws minimal power |
Common errors | Considerable observational errors | Free from observational errors |
Measuring pH is critical in many industries such as the importance of measuring pH in wine-making. So, if you’re examining the pH of water or brewing beverages like wine, opting for a digital sensor could be advantageous for obtaining immediate results. For well-suited projects where only two voltages are needed, digital sensors are best.
On the other hand, if continuous signals are essential, an analog sensor might be the more suitable choice.
Both analog and digital sensors continue to play a vital role in various industries and applications. While analog sensors excel in situations that require precise measurements and continuous data representation, digital sensors are preferred when accuracy, reliability, and compatibility with digital systems are paramount.
If you are unsure which sensor is best for your application or what digital sensors we have to offer, do not hesitate to contact the world-class team at Atlas Scientific.
Finding the best pH probe for hydroponics can make or break your growing success. In hydroponics, maintaining the correct pH is essential because it directly
The fastest way to reduce ammonia levels in a fish tank is to perform partial water changes, temporarily stop feeding fish, use chemical filtration, increase