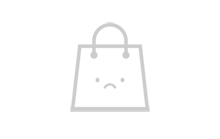
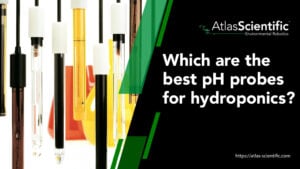
Best pH Probes For Hydroponics in 2025 – A Complete Buying Guide
Finding the best pH probe for hydroponics can make or break your growing success. In hydroponics, maintaining the correct pH is essential because it directly
# Type at least 1 character to search # Hit enter to search or ESC to close
No products in the cart.
No products in the cart.
Product Categories
Dissolved oxygen measurement is essential for monitoring water quality in various applications. It’s used in wastewater treatment to ensure optimal conditions for bacteria, in aquaculture to maintain healthy fish populations, and in environmental monitoring to assess ecosystem health. Additionally, it’s crucial for laboratory research, drinking water treatment, and industrial processes requiring precise oxygen levels.
Accurate dissolved oxygen (DO) monitoring stands as a cornerstone of quality control and process optimization across multiple industries. We rely on precise sensor applications to maintain optimal dissolved oxygen levels that directly impact product quality, process efficiency, and regulatory compliance.
From ensuring the survival of aquatic life to maintaining beverage quality, dissolved oxygen measurement applications play a vital role in modern industrial processes.
Dissolved oxygen applications often work alongside temperature sensor applications and other monitoring systems to provide comprehensive process control. The integration of these sensor network applications helps us maintain precise oxygen levels while ensuring consistent product quality and process efficiency.
In this guide, we will explore the essential aspects of dissolved oxygen measurement applications, examine specific industrial applications, compare measurement technologies, discuss implementation best practices, and provide troubleshooting strategies.
We encounter diverse dissolved oxygen measurement applications across various industries, each with unique requirements and challenges. As we advance in technological sensing, applications have evolved to meet these specific needs, providing precise monitoring and control capabilities.
In wastewater treatment, dissolved oxygen levels are maintained at 2 mg/L during secondary treatment to support crucial bacterial processes.
Dissolved sensors help monitor these levels continuously, ensuring optimal conditions for biological treatment. When DO levels exceed 5-6 mg/L, we often find it indicates potential problems with mechanical mixer rates, which could damage the activated sludge process.
Fish farming operations require our most sensitive dissolved oxygen measurement applications, as aquatic life depends on precise oxygen control. Dissolved oxygen levels are maintained between 5-6 ppm for optimal fish growth and activity. Our temperature sensor applications work alongside DO sensors to provide comprehensive environmental monitoring, as oxygen solubility varies significantly with temperature changes.
Key factors monitored in aquaculture systems:
In brewing applications, we focus on controlling total package oxygen (TPO) to ensure product quality and stability.
Measuring dissolved oxygen in wine is crucial to ensure the taste and longevity are correct. Red wines typically have dissolved oxygen (DO) levels below 1.25 mg/L, while for white, blush, and rosé wines, the DO level is kept below 0.6 mg/L.
To ensure an efficient brewing process, water should have minimal dissolved oxygen to avoid contamination and oxidation during brewing, packaging, and storage. Even small amounts of dissolved oxygen can cause beer to develop a stale, musty taste and smell, and in severe cases, make it undrinkable. Therefore, closely monitoring low dissolved oxygen levels with a DO meter is a crucial part of brewing.
The dissolved oxygen level should not exceed 0.05 mg/L or 0.05 parts per million at any stage of the brewing process. For smaller operations, a regular dissolved oxygen kit can be used, while for larger brewing operations, we recommend using the Industrial DO kit for in-line dissolved oxygen monitoring.
Selecting the right measurement technology forms the foundation of successful dissolved oxygen monitoring.
Two distinct measurement technologies are typically used in dissolved oxygen applications.
Optical sensors utilize luminescent technology, where oxygen molecules interact with specialized dyes in the presence of blue light.
In contrast, electrochemical sensors employ either galvanic or polarographic cells to measure oxygen concentration through electrical current generation.
Feature | Optical Sensors | Electrochemical Sensors |
Response Time | 40 seconds avg. | 20 seconds avg. |
Calibration | Maintains for months | Requires frequent calibration |
Power Usage | Higher consumption | Lower consumption |
Maintenance | Annual cap replacement | Bi-annual membrane change |
We consider several critical factors when recommending sensor applications:
Dissolved oxygen measurement applications frequently integrate with broader control systems. Both analog and digital signal processing methods are implemented, connecting sensor network applications to various control units.
For optimal performance, we recommend using Electro-Optical Modules (EOM) when incorporating optical sensors into existing control systems, ensuring seamless data transfer and reliable measurements.
At Atlas Scientific, we have a range of dissolved oxygen to suit your application, whether that be our updated Industrial Dissolved Oxygen Sensor, Mini Lab Grade DO Probe, Lab Grade DO Probe, or our latest EZO Complete Dissolved Oxygen Kit – the perfect solution for hassle-free dissolved oxygen monitoring.
Successful implementation of dissolved oxygen measurement applications requires careful attention to installation, calibration, and maintenance procedures. Our years of experience with sensor applications have taught us the critical importance of following established best practices.
When implementing dissolved oxygen sensor applications, you should prioritize location selection to allow easy access for maintenance while ensuring accurate measurements.
We recommend mounting sensors at a slight angle to prevent air bubble accumulation, which can cause false readings. The sensor must be completely submerged, and we always run cables through protective conduits to prevent moisture intrusion and signal distortion.
Our recommended calibration approach follows a systematic process that ensures consistent readings across all our dissolved oxygen measurement applications:
Step | Action | Key Consideration |
1. Preparation | Clean sensor with distilled water | Remove all residue |
2. Zero Point | Immerse in zero oxygen solution | Allow stabilization |
3. Span Check | Calibrate in air-saturated water | Monitor temperature |
4. Verification | Compare measurements with known standards | Document readings |
Calibration should be performed every month. However, harsh environments may require more frequent attention.
Regular maintenance is crucial for the optimal performance of sensor network applications. We recommend the following:
We recommend replacing the sensing cap annually for optical sensors, while electrochemical sensors require membrane replacement every six months. Your maintenance schedule should always be adapted based on the specific application requirements and environmental conditions.
Through our extensive work with sensor applications, we’ve identified that troubleshooting and optimization are critical for maintaining accurate dissolved oxygen measurements.
We frequently encounter several key issues in our dissolved oxygen measurement applications. Our experience shows that understanding these challenges is crucial for maintaining optimal performance:
Challenge | Cause | Solution |
Calibration Drift | Temperature fluctuations, membrane aging | Weekly verification, temperature compensation |
Air Bubble Interface | Improper installation, high turbulence | Adjust mounting angle, implement bubble traps |
Chemical Interference | Presence of H2S, chlorine | Install specialized membranes, regular cleaning |
Signal Instability | Background electrical noise | Improve grounding, shield cables |
Always maintain measurement accuracy through the following:
Regular Calibration Checks:
For accurate dissolved oxygen measurements, it’s recommended to perform weekly calibration checks against known standards. Any deviations greater than ±0.2 mg/L should be documented and addressed.
Additionally, temperature compensation should be factored into these checks to ensure precise readings.
Performance Tracking:
Tracking the sensor’s response times and monitoring for drift patterns can provide valuable insights into its performance over time. Keeping detailed records of these metrics will help predict when maintenance may be needed and allow for the optimization of calibration intervals.
Validation Testing:
Monthly validation testing using different measurement methods (such as manual titration or alternate sensors) is crucial for cross-verification. If there’s a discrepancy greater than 2% between methods, it’s important to investigate possible sources of interference and adjust measurement protocols to account for these factors.
By consistently implementing these practices, individuals and teams measuring dissolved oxygen can improve the reliability and accuracy of their measurements, reduce the need for frequent maintenance, and ensure more consistent, dependable results across a range of applications.
Accurate dissolved oxygen measurement stands as a critical requirement across numerous industries, directly impacting product quality and process efficiency. These measurements play in wastewater treatment, aquaculture, and beverage production.
We examined key measurement technologies, comparing optical and electrochemical methods while highlighting their specific advantages. Through proper implementation of best practices, regular maintenance, and systematic troubleshooting, you can achieve reliable dissolved oxygen monitoring.
If you would like to learn more about dissolved oxygen measurements, or what dissolved oxygen sensor will best suit your application, do not hesitate to contact the world-class team at Atlas Scientific.
Finding the best pH probe for hydroponics can make or break your growing success. In hydroponics, maintaining the correct pH is essential because it directly
The fastest way to reduce ammonia levels in a fish tank is to perform partial water changes, temporarily stop feeding fish, use chemical filtration, increase