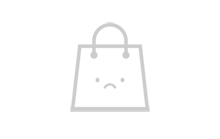
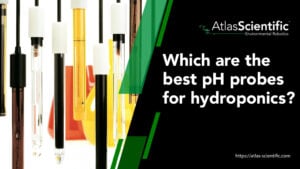
Best pH Probes For Hydroponics in 2025 – A Complete Buying Guide
Finding the best pH probe for hydroponics can make or break your growing success. In hydroponics, maintaining the correct pH is essential because it directly
# Type at least 1 character to search # Hit enter to search or ESC to close
No products in the cart.
No products in the cart.
Product Categories
Dissolved oxygen (DO) probes are key components in bioreactors, ensuring optimal conditions for cell growth and biochemical reactions. These specialized sensors measure and monitor the oxygen levels within the bioreactor, providing the user with real-time data to maintain ideal oxygen levels. Proper oxygen levels are vital for maximizing cell health, yield, and productivity in bioprocesses such as cell culture and fermentation. Effective oxygen control not only improves bioreactor performance but also reduces risks such as oxygen depletion or oversaturation. Therefore, dissolved oxygen probes are indispensable tools for high-quality and efficient bioproduction in bioreactors.
Dissolved oxygen (DO) is an important parameter that determines the success of bioprocesses within bioreactors. Whether that be cultivating mammalian cells, producing biochemical substances, or fermenting microorganisms to brew beer, controlling and maintaining DO levels is fundamental. However, these microbial strains and cell lines have specific oxygen level limits, demanding precise monitoring and control systems.
A bioreactor is a system designed to create an optimal and controlled environment for biological and chemical reactions, facilitating the growth of microorganisms, cells, tissues, and algae. Widely used across industries like biotechnology, pharmaceuticals, food production, and wastewater treatment, bioreactors are valued for their efficiency, cost-effectiveness, and precise control over growth conditions.
Different fermentation processes and cultures require specific oxygen conditions.
Aerobic Cultures
These cultures are essential for mammalian cell cultures and many microbial cultures including E. coli. Aerobic cultures generally need a DO concentration above 30%. This high DO level supports robust cell growth and metabolism, leading to a productive production process.
Anaerobic Fermentation
As the name suggests, this process occurs when there is no oxygen. Anaerobic microbes that thrive in oxygen-free environments that are also important for producing chemicals include lactic acid, ethanol, and acetic acid. Accurately measuring DO levels helps prevent any unintended oxygen interference, which could disrupt chemical production.
Microbial Fermentation
This process involves lower DO concentrations and is commonly used in bacterial fermentation such as producing probiotics and cultivating lactic acid bacteria. The low DO concentration is key for microbial activities.
To achieve optimal culture growth and high productivity, maintaining accurate DO levels is vital. The growing cells inside a bioreactor continuously consume oxygen, which demands a robust dissolved oxygen control system. A typical system involves many components that work together, including:
Efficient DO control requires deep understanding and the optimization of key parameters.
A DO cascade is a control strategy that defines the sequence of actions the bioreactor takes to maintain stable oxygen levels. In a typical cascade system, various actuators like impellers and gas spargers are adjusted in a pre-defined order based on the DO readings.
For example, an increase in agitation might be the first step to raise DO levels, followed by increased airflow, and lastly, the introduction of pure oxygen if needed.
Spargers play a critical role in controlling DO levels by introducing gases into the bioreactor. The type of sparger can significantly influence gas transfer efficiency:
Selecting the right sparger type depends on the specific needs of the bioprocess, such as whether fine control over DO levels or rapid degassing is required.
The composition and flow of gases introduced into the bioreactor significantly affect the DO environment:
Effective DO control relies on a nuanced understanding of how different gases interact with the bioreactor’s microbial environment.
Impellers not only promote efficient mixing but also influence oxygen transfer rates:
The choice of impeller directly impacts the oxygen transfer rate (OTR) and overall mixing efficiency, making it a critical consideration for DO control.
In bioprocessing, “100% DO” refers to the saturation point of oxygen in the medium, where the liquid can hold no more dissolved oxygen under specific conditions. It’s important to distinguish this from the absolute oxygen concentration, which varies with temperature, pressure, and salinity. Proper calibration of DO probes ensures that readings reflect the true oxygen availability for the cultured cells.
Choosing the right DO sensor can significantly influence measurement accuracy and reliability. Here are two types of dissolved oxygen probes, mainly used in bioreactors:
Optical sensors are becoming increasingly popular due to their robustness and reduced need for frequent calibration.
Two critical parameters, kLa (volumetric mass transfer coefficient) and OTR (oxygen transfer rate) are essential for understanding and optimizing oxygen dynamics in bioreactors:
By monitoring kLa and OTR, bioprocess engineers can fine-tune bioreactor conditions to optimize oxygen availability for cell growth.
Advanced bioreactor control systems, like those from Eppendorf, provide comprehensive solutions for DO management:
The importance of dissolved oxygen monitoring extends beyond traditional bioreactors:
Accurate DO readings are vital for maintaining optimal conditions. Here are some common sources of error and how to avoid them:
Proper maintenance of dissolved oxygen probes extends their lifespan and ensures accurate measurements:
To achieve high productivity and consistent results in bioprocessing, accurate DO measurement and control are non-negotiable.
Utilizing advanced DO probes like those from Atlas Scientific provides the reliability needed for sophisticated bioreactor systems. By combining cutting-edge sensors with optimized DO control strategies, bioprocess engineers can ensure that their cultures thrive under ideal conditions.
As bioprocessing technologies evolve, the role of dissolved oxygen probes will continue to expand. With the increasing complexity of cell cultures and the demand for higher yields, precise DO control is more critical than ever.
If you would like to learn more about dissolved oxygen in bioreactors or what dissolved oxygen would best suit your system, do not hesitate to contact the world-class team at Atlas Scientific.
Finding the best pH probe for hydroponics can make or break your growing success. In hydroponics, maintaining the correct pH is essential because it directly
The fastest way to reduce ammonia levels in a fish tank is to perform partial water changes, temporarily stop feeding fish, use chemical filtration, increase
Notifications