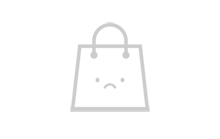

Everything You Need To Know About Sensor Housing
Sensors play a crucial role in collecting critical data in the world of scientific measurement and industrial monitoring systems. However, a sensor’s reliability and lifespan
# Type at least 1 character to search # Hit enter to search or ESC to close
No products in the cart.
No products in the cart.
Product Categories
There are four main temperature sensors used today in modern-day electronics: Negative temperature coefficient (NTC) thermistors, resistance temperature detectors (RTDs), thermocouples, and semiconductor-based integrated (IC) sensors.
Temperature sensors are essential to everyday life. They measure the amount of heat a system or object gives off, typically setting off an alarm when a temperature change exceeds the application’s guidelines. Therefore, temperature sensors play a critical role in providing time for preventative action.
In this article, we will look at the four main temperature sensors, the considerations for each, and the advantages and disadvantages of using them.
A temperature sensor is an electrical instrument that measures the temperature of the air, liquid, and solid matter in a wide range of industries and applications.
A temperature sensor works by providing a readable temperature measurement on a meter from electrical signals produced inside a temperature probe. The working principle of a temperature sensor depends on the voltage across the diode inside the temperature probe. The change in temperature is directly proportional to the diode’s resistance. For example, the warmer the temperature, the more resistance, and vice-versa.
At Atlas Scientific, we often get asked this question. A temperature sensor solely outputs temperature measurements in a digital or analog format to another device, such as a microprocessor, which uses temperature to control equipment.
On the other hand, a thermostat integrates a temperature sensor with a switch or valve.
Temperature sensors are key to gathering temperature data, but they don’t directly affect temperature themselves. However, temperature controllers are active components that both receive temperature information from sensors and use this data to make decisions that regulate the system’s temperature.
Temperature sensors are extremely useful to cater to both commercial and consumer needs, which is why they are used in the following industries and applications:
Temperature sensors fall into two categories – contact and noncontact temperature sensors. These are then classified into different subtypes, giving us the four types of temperature sensors used today.
Contact temperature sensors are used when you can make good thermal contact with an object, liquid, or gas. They are used to identify the temperature when it is expected below 3400 °F (1700 °C) or above -40 °F (-40 °C).
Contact temperature sensors include thermistors, thermocouples, and resistance temperature detectors.
As the name suggests, non-contact temperature sensors do not have to be in direct contact with what you are measuring. Instead, they use infrared technology to measure the surface temperature remotely.
They are used when:
Non-contact temperature sensors include fiber optic sensors, radiation thermometers, optical pyrometers, and thermal imagers.
There are four common temperature sensors used in the market today:
Resistance temperature detectors, or RTDs, change the resistance of the RTD element directly with temperature. RTDs are made from a film and a glass or ceramic core with wire wrapped around it for greater accuracy. While platinum RTDs (PRTDs) are more expensive, they are the most accurate temperature sensor. In addition to high accuracy, PRTDs offer stable readings, repeatable responses, and they can be used over a wide temperature range (-200 to 600 °C).
Platinum RTDs are available with a 100 Ω and 1000 Ω resistance at 0 °C, which is why they are referred to as PT100 and PT1000.
RTD sensors that are made from nickel and copper are also used because of their lower cost, but, they are not as stable or repeatable as PRTDs.
Compared to other types of temperature sensors, RTDs typically have higher thermal mass, and therefore they usually respond slower to temperature changes than thermocouple temperature sensors. RTDs also require an excitation current to flow through the meter to calculate the resistance. Converting the resistance into an actual temperature reading can be challenging. Thankfully, the Atlas Scientific EZO-RTD Circuit simplifies the process, allowing users to obtain highly accurate measurements from platinum RTD probes with ease.
RTD sensors are categorized according to how their temperature sensing elements are constructed. The two primary types are thin film and wire wound. The type of RTD sensor used depends on the specific conditions and purpose of its intended use. temperature-sensing
RTD configurations include two, three, and four-wire options:
Thermistors are similar to RTDs, as the resistance varies with temperature. As thermistors have a non-linear temperature relationship, they require correction to interpret the data accurately. This relationship means that thermistor temperature sensors can supply a large resistance variation over a small temperature working range, which is why they are used for measuring temperature in high-tech and set-point applications.
They are typically made from polymer or ceramic covered in a glass surface, which is why they are cheaper and less accurate than RTDs. Thermistors are, however, still accurate compared to other types of temperature sensors, because of their repeatability and quick response to variations in temperature.
Negative temperature coefficient (NTC) thermistors are the most commonly used thermistor to measure temperature. An NTC thermistor’s resistance decreases when temperature increases. Glass-encapsulated thermistors have an operating range of -72.4 to 482 °F (-50 to 250 °C) and standard thermistors have a range of up to 302 °F (150 °C).
Thermocouple temperature sensors are the most commonly used in industrial, automotive, and everyday applications in your home. As they are self-powered, they require no excitation, have quick response times, and they can operate over the widest temperature range (-328 to 3182 °F/-200 °C to 1750 °C.).
Thermocouples are made by joining two dissimilar metal wires, electrically bonded at two points. The connecting end is called the “hot junction”, and the other end is known as the “cold junction”. The varying voltage between the two metals mirrors proportional changes in temperature.
The working principle is very simple. When the two dissimilar metal wires are fused, they create a thermoelectric result, which provides a constant potential difference. The voltage between the metals is called the “Seebeck effect”. If both parts have the same temperature, the potential difference is zero, and therefore, has no output voltage. But, when the parts have different temperatures, the output voltage is relative to the temperature difference.
Thermocouples are made from a variety of different materials, allowing the temperature sensor to measure different temperature ranges and sensitivities. The most common thermocouple sensor used is the K-type, and all other thermocouples are also designated using letters (J, R, and T).
The biggest disadvantage to using a thermocouple sensor is its small output voltage, making it challenging to measure the temperature of the object or substance. Because of the small voltage and cold junction compensation (CJC), thermocouples require precision references with low noise, and often some amplification solutions are needed.
As thermocouples are also non-linear, they require a conversion table to work out the temperature.
Semiconductor-based temperature sensors are typically incorporated into an integrated circuit (IC). The two identical diodes with temperature-sensitive voltages monitor temperature changes. Integrated circuit sensors have a linear response, however, they have the lowest accuracy of temperature sensors. This is because ICs have the slowest response across narrow temperature ranges (- -70 °C to 150 °C).
There are two types of ICs:
If you require the most accurate temperature sensor, an RTD is the best choice. RTD temperature sensors are the most accurate and stable electronic devices for measuring temperature. Here at Atlas Scientific, we only offer high-quality platinum RTD temperature sensors to always provide you with highly accurate readings and low latency.
Depending on which application or industry you work in, will depend on which temperature sensor to use. Platinum resistance temperature detector (PRTD) sensors are the most accurate, yet, negative temperature coefficient (NTC) thermistors, thermocouple sensors, and semiconductor-based integrated sensors (ICs) are also widely used.
If you have any questions regarding temperature sensors or are unsure which temperature sensor will best suit your needs, please do not hesitate to contact the world-class team at Atlas Scientific.
Sensors play a crucial role in collecting critical data in the world of scientific measurement and industrial monitoring systems. However, a sensor’s reliability and lifespan
Advanced industrial water quality monitoring is critical for process optimization, regulatory compliance, and equipment protection, providing real-time insights, multi-parameter tracking, and system integration that save
Notifications